www.foodpackautomation.com
27
'24
Written on Modified on
BOBST News
Geostick creates an agile future with BOBST DIGITAL MASTER 340 all-inline automated label press
Geostick Group, operating from its state-of-the-art facility in Uithoorn, the Netherlands, is a premier supplier of self-adhesive labels, flexible packaging, and printing solutions.
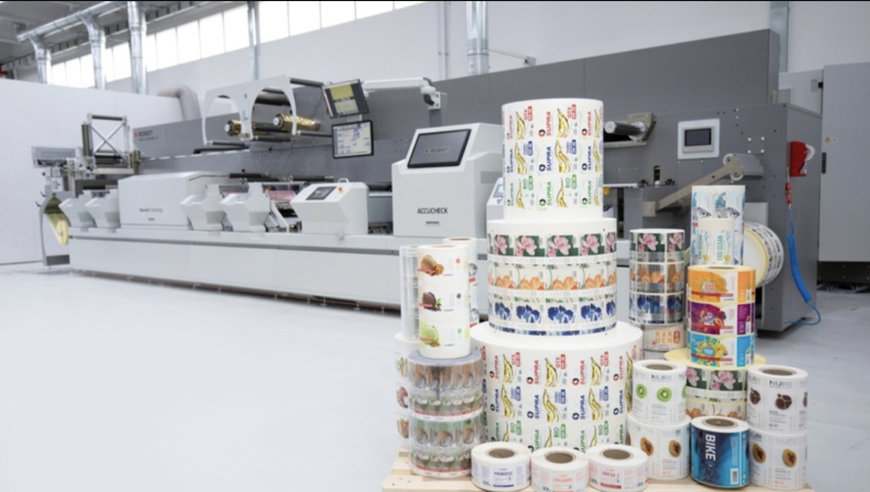
In addition to providing exemplary service levels, the business has a strong focus on label industry sustainability, focusing on low-carbon material innovation, low migration inks and comprehensive ISO certification. To push its capacity and capabilities further than ever before, Geostick invested more than a year ago in a BOBST DIGITAL MASTER 340 label press, an all-in-one, all-inline label press that works as a fully digitized and automated production line, from printing to embellishment and die-cutting.
Cees Schouten, Operations Director (COO) at Geostick, believes that inkjet technologies have a profound place in the future of agile label printing, and explains the decision to invest in the BOBST machine: “For our team, partnering with BOBST was a clear choice. The DIGITAL MASTER 340 label press is our first BOBST equipment, but the company’s good reputation across the industry is well-known”.
“A core development focus for our operations, like many businesses in our industry, lies in automation. By creating a more connected workflow, we not only improve efficiency but empower our operators to accomplish more. This is why we have become an early adopter of the pioneering BOBST DIGITAL MASTER 340 inkjet technology and we’re already seeing positive results”.
The All-in-One press DIGITAL MASTER 340 showcased at Labelexpo Europe, offers printing, embellishment and die-cutting functions in a single pass, with seamless integration between the UV inkjet digital engine, the automated flexo units, and the embellishment and converting modules, granting flexibility and infinite applications output to the converter.
Designed for speed, the press runs at up to 100 m/min in four or six colours plus optional digital white, and effortlessly bridges the gap between traditional digital and flexo machines. The DIGITAL MASTER series modular architecture enables label converters to configure the exact machine they need and can be upgraded on-site at any point.
Mr Schouten adds: “The key to staying competitive is automation, so label presses must be designed with this in mind – and that’s an area where BOBST shines. The technology is so new, we’re on a learning curve, but after just half a year we’re seeing very promising results in our daily and monthly output. We see an increase in digital label production, so we are excited to see how far we can push the technology with BOBST’s ongoing support”.
www.bobst.com