Making the Switch from Manual to Semi-Automated Case Forming and Packing
Replacing traditional manual hand case packing in secondary packaging lines with semi-automated systems can provide the perfect fit for operations which are just starting to automate.
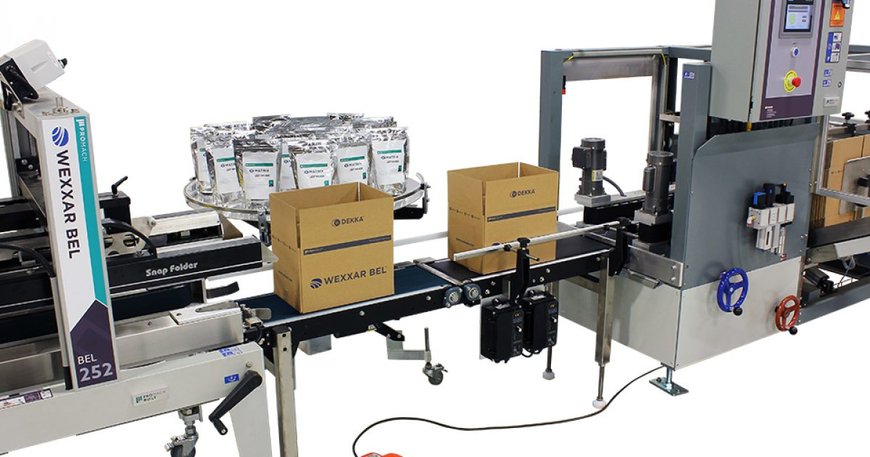
At a fraction the cost of fully automatic case erectors and packers, semi-automated systems, like the Model 505V2 from Wexxar Bel, provide an economical and effective way of streamlining throughput while reducing manual labor.
From big manufacturers to small production shops, the desire to run more efficient packaging operations and cut costs is universal. But these companies have one strategy in common – they are all upgrading their packaging processes to better utilize their production capacity, and make their operations run faster, smoother and with a heightened return on their investment. To that end, upgrading case forming and packing in their secondary packaging processes from manual to semi-automated systems can provide considerable efficiencies to their operations.
Production Capacity
Because case packing is integral to virtually all manufacturing processes, an accurate assessment of case throughput capacity is essential. Any increase in production volume requirements, when relating to secondary packaging, is often the key driver that necessitates the move to more efficient systems. Where cost reduction is a considerable factor, it too, along with increases in volume throughput, must be factored into the production capacity equation.
Manufacturers will typically scale the sophistication of their packaging processes to meet these requirements. In most high-volume packaging environments, for example, automated and semi-automated packaging applications may be in use, dependent on the throughput volumes and labor requirements at any stage in the packaging process. Capacity decisions affect production lead time, operating costs, and essentially, the manufacturer’s ability to profitably compete.
Manual or Semi-Automated Case Forming and Packing
Viewing case packing from a production capacity perspective, there are a number of factors that would support adopting a more efficient, semi-automated system as a better business solution. A good example of such semi-automated case packing is the Model 505V2 case packer, engineered by Wexxar Bel. For almost 50 years the company has been a leading manufacturer of automated case erectors for consumer product packaging applications. This latest generation of machines is focused squarely on increasing flexibility and throughput by automating what previously required manual operation.
This is strictly a semi-automatic case forming system. The operator pulls the case open from flat, and pushes it down into the machine. The bottom of the case is folded and held in place, so the operator could potentially load at this point, and then move it on for sealing.
Here are factors inherent in this case packer that directly influence a more efficient production capacity:
- Ergonomic Two-Handed Packing – holds the case in place for quick and ergonomic case packing. This is much more efficient than a traditional hand pack line.
- Precision Dynamic Flap Folding – mechanical flap folding ensures cases are consistently square, even with softer or recycled corrugated.
- Smooth Transfer of Filled Cases – formed cases are positioned on a roller deck for easy transfer into case sealing.
- Quick Changeovers – on-machine pictorial guides with dual lead screws for easy size changes from either side.
- Compact Designs – small machine footprint saves valuable floor space and removes the time and space consuming process of pre-forming cases.
Optimized Electro-Pneumatics
The use of electro-pneumatic switches and folders provide a precise and quiet fold. This allows the machine to excel in applications featuring more unique or less traditional case styles. The manual switches have non-contact sensors, allowing for a higher precision fold, fewer wear parts on the machine, and better performance on softer recycled corrugated.
Conventional pneumatic-operated semi-automated case formers/packers employ multiples of 4-way valves connected to air hoses and the performing machine components. Each of these connections is a potential source of air loss. The latest designs of case packers incorporate centralized pneumatic components which reduce air leakage by as much as 27 percent, making for a considerable reduction in energy usage.
Faster Cycle Times, Reduced Cost of Operation
As these semi-automated case packers evolve, like the state-of-the-art Model 505V2, they are improving on machine controls so the systems cycle faster, likewise making fine improvements in how the machines are set up to operate and interact with human operators. These factors equate to leverage production capacity to more optimum levels. This means better production throughput, faster ROI and better profitability.
www.wexxar.com