www.foodpackautomation.com
01
'23
Written on Modified on
Dunkermotoren News
Fresh to the shelf thanks to efficient packaging lines with Dunkermotoren
To get fresh food to the shelves as quickly as possible, it must be processed and packed very fast. Innovative motor solutions in hygienic design provide packaging machines with maximum flexibility for all applications.
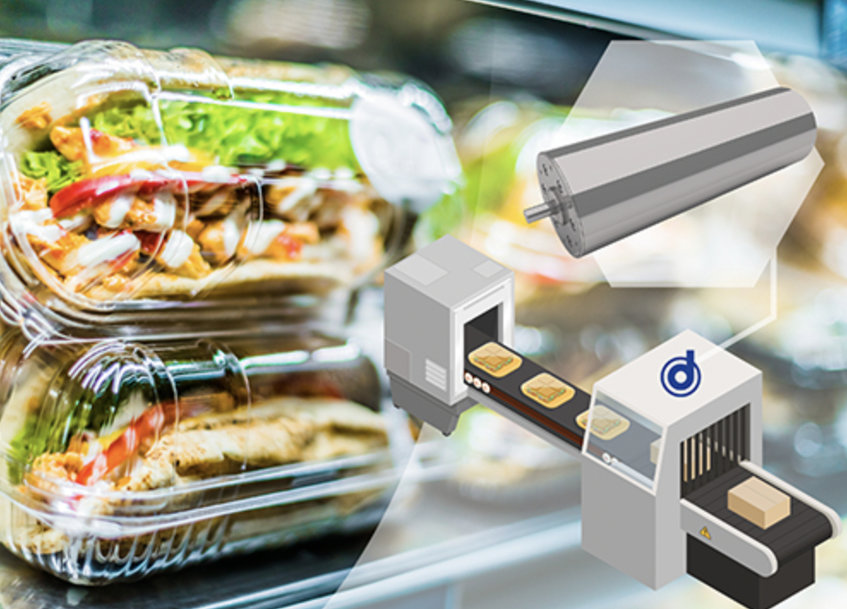
How do you decide which products end up in your shopping bag during your weekly shopping? The price is for sure the most important factor, followed by the longest possible shelf life. But how does fresh food get to the shelves of our discounters so quickly?
Innovative weighing, labelling, and packaging lines in the food industry ensure that food products can be quickly and safely packed and shipped to discounters and other retailers. Intelligent and highly efficient drive solutions installed in those systems provide the necessary speed and flexibility. At the same time, they must meet the high requirements in the food and beverage industry and enable hygienic cleaning.
With a modular product portfolio provides Dunkermotoren, a brand of AMETEK, individually configurable drive solutions for all areas in primary, secondary and transport packaging.
Hygiene – the Alpha & Omega in food processing and packaging
To meet the high requirements in the food and beverage industry, the drive technology manufacturer offers both its rotative brushless DC motors and highly precise linear motors with special stainless-steel housings.
The design with its smooth surface allows easy and thorough cleaning. The material is exceptionally resistant to corrosion and does not suffer damage even from frequent contact with disinfectants or detergents. Thus it is particularly well suited for use in food processing. Especially when raw foods are portioned, weighted, and packed, thorough cleaning of the machines is essential. Stainless steel is very robust and ensures bacteria and fungi not to adhere.
The Dunkermotoren linear motor series SL 38 STL (stainless-steel) is the perfect match for packaging, bottling and transfer systems in the food industry. With an acceleration of over 200 m/s2, the stainless-steel solution can bring the system output to a maximum and works extremely precisely. Combined with special glands and hygiene seals it allows protection classes up to IP69K and prevents splash water from penetrating the motor while cleaning the system.
For maximum flexibility and a changeover to alternative product and packaging formats during operation, it should be used the intelligent BLDC motor series. Motion profiles and parameters can be easily programmed in C via the Dunkermotoren Motor Control Platform (MCP). Since the electronics is fully integrated into the motor housing, the drive solution can be installed inside the packaging machine and can communicate to a higher-level controller via CANopen or Ethernet interfaces such as EtherCAT, Ethernet/IP and PROFINET. The configured solution including motor, electronics, gearbox, brake, and encoder can optionally be built in a continuous stainless steel housing, allowing the drive to meet the hygiene and design requirements in the primary packaging sector.
Speed and intelligence ensure freshness and competitive pricing
Compared to slowly working screw drives, linear motors can reduce the production costs of a product significantly. On the one hand, the acquisition costs are higher than for alternative drive concepts. But, on the other hand, its extreme speed and positioning accuracy ensure a maximum output of the bottling or packaging process, thus resulting in lower costs and competitive pricing. Additionally, the high speed of modern bottling and packaging lines lead to shorter cycle times so that fresh food can be shipped faster to discounters and retailers. You as a consumer, in turn, benefit from a long shelf life and special freshness.
When intelligent BLDC motors with integrated motor electronics are used, smart services from the IIoT brand nexofox enable features such as real-time monitoring and alert management which allow an optimized motor operation in terms of minimized wear. An analysis of operating data additionally offers the possibility to early detect maintenance requirements and prevents machine failures which could lead to the destruction of entire batches, in the worst case.
Thanks to decades of experience with always new, challenging projects for food processing and packaging, Dunkermotoren and nexofox can offer its customers field proven state-of-the-art solutions to manage the challenges you are facing for your application – today and in future.
www.dunkermotoren.com